The Ultimate Guide to Business Process Mapping
Process Mapping is the core component of Business Process Management. It is the best way to capture your business processes, so that you can share, use and improve them. Triaster have been refining our process mapping software and services for over 20 years and there is not a lot we don’t know about it.
In this Ultimate Guide to Business Process Mapping we share our knowledge with you, including how process mapping is the first step to Continuous Improvement.
If there is anything else that you would like to ask about Process Mapping, or if you would just like to speak with us, please call us on +44 (0)207 770 8053 or e-mail us at info@triaster.co.uk – we would love to hear from you.
What is Process Mapping?
Understanding Process Mapping
The Key Components of Process Mapping Projects
Process Mapping Tips and Tools
How to Process Map – a Step-by-step Guide
Using Triaster for Continuous Business Improvement
Chapter 1 - What is Process Mapping?
Process mapping is an exercise undertaken to capture process data in diagrammatic form for the purposes of business process improvement.
The aim of process visualisation (mapping) is to capture the current business process as it is currently being performed and create a step-by-step layout of all the process steps. From here, improvement opportunities can be identified so that at a later time, change can be implemented.
A process map will typically:
- Describe the flow of materials, information and documents
- Show the tasks contained within the process
- How a specific task transforms inputs into outputs
- Show decisions that need to be made along the chain
- Demonstrate the relationship between process steps (using symbols/shapes); and reminds us that the strength of a chain depends upon its weakest link

Why Use Process Mapping?
The most crucial ongoing activity in any business is to identify three states within the business:
- Where are we now?
- Where do we want to be?
- How do we transform from where we are now to where we want to be?
By keeping an eye on these three questions, an organisation can constantly re-evaluate their efforts and whether those efforts are leading them to desired outcomes.
Just like it would be difficult to find a destination without a map, a path and road markers, it is difficult to reach improvement goals without process mapping; also, just as multiple factors help a traveller to find a destination (map, path, road markers), so too does process mapping include symbols and connectors to help an organisation visualise the entire process journey step-by-step.
The map of an organisation's current state forms a simple and accurate picture of current operations and offers insights into how to reach greater efficiency gains - which is why this is one of the best return on investment activities an organisation can take up.
This then allows an organisation to:
- Evaluate improvement opportunities
- Implement a standard way of working throughout the company (meaning that employees will perform a process the same way)
- Ensure quality
- Assign each process step with a level of risk
- Retain employee knowledge when an employee decides to leave
- Increase customer satisfaction
It also stops an organisation from:
- Blindly making system changes that lead to costly mistakes
- Employing inefficient employees who waste time due to existing problems in the process chain
- Continuing to perform wasteful processes
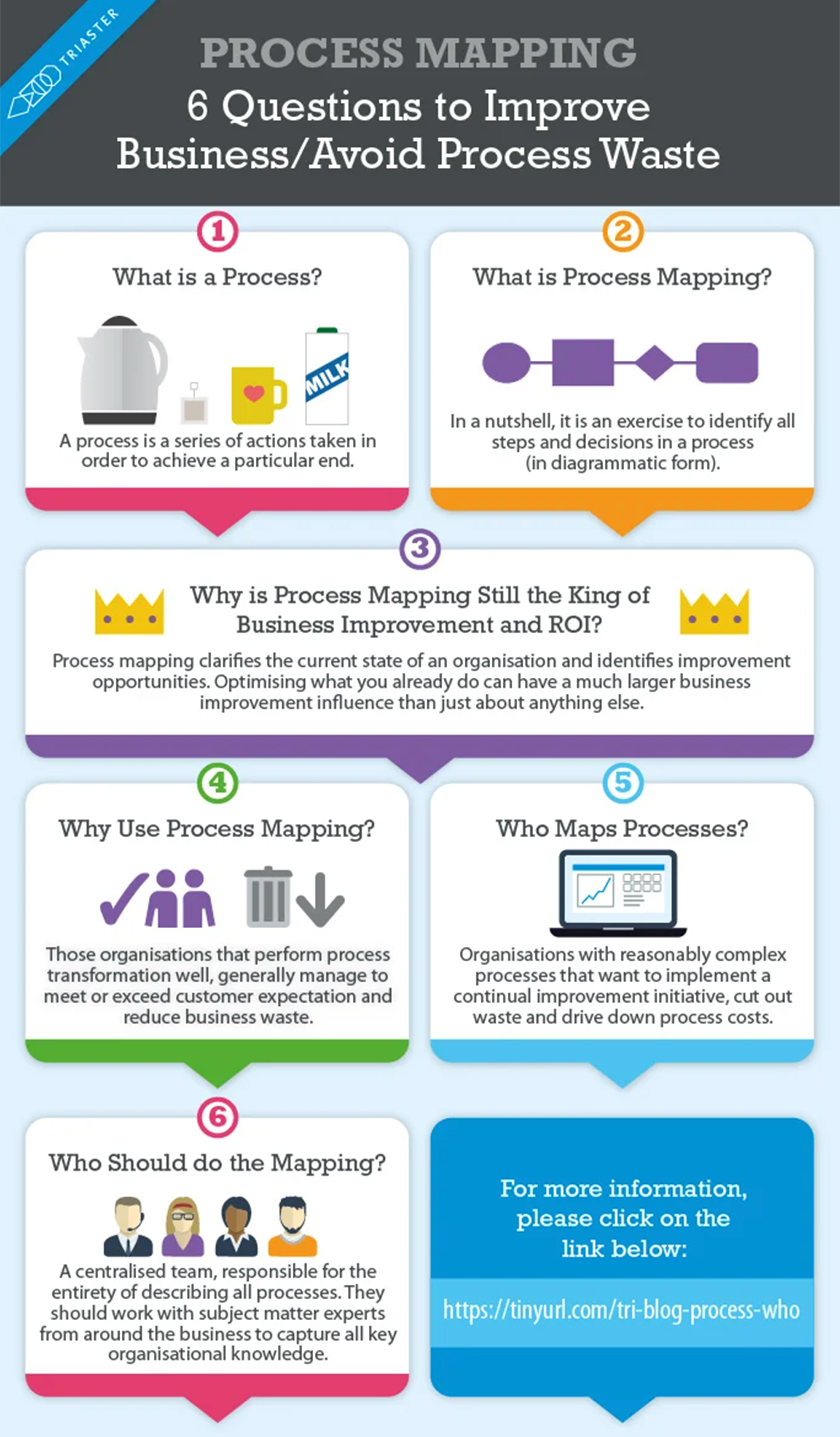
What is Value Stream Mapping?
Value Stream Mapping, like process mapping, is used to visualise the product pipeline as a series of process connections.
The emphasis of this type of mapping is in measuring the value that those steps bring to the customer.
Value stream maps are used to visualise and identify delays, restraints and excessive inventory within processes. There are three groups within the value stream...
- Value Adding – a customer is willing to accept this step as an acceptable cost to them
- Non-value Adding – the customer feels it unfair to assign these costs to them
- Necessary Non-value Adding – costs to the customer are necessary but the customer may still feel unhappy to pay
Value stream mapping is still process mapping, but with a focus toward always asking the question:
'Is this process adding value to the customer?'
and;
'If it is not adding value, is it still necessary to keep the non-value adding process and assign the costs to the customer?'

Chapter 2 - Understanding Process Mapping
8 Benefits of Process Mapping
Process mapping originated in the early 1920s and the concept has survived ever since due to the structured effect that process flow diagrams have had on creating efficient working environments. Even so, most organisations don't understand the benefits of mapping business processes.
1. Visibility of Your End-to-end Processes
End-to-end process mapping simply means visualising that process from the very start to the very finish (example: customer order through to customer delivery). This helps to break down silos by giving employees visibility of the process journey, which encompasses both other business areas and the eventual use by the end user. Seeing a process from end-to-end helps employees understand where they fit within the organisation and how they work as a cross-functional team.
2. Creating Evidence Based Change
As I have previously stated, any business change must be thoughtfully considered with two simple questions:
'Where do we want to be?'
and;
'Where are we now?'
The answer to the first question doesn't require a lot of work (considering it is a goal), the answer to the second requires analysis of your current state or the As-Is process. You can then use this as a baseline to model your future state (To Be variants).
Process mapping tools will also store meta-data such as cost, total effort and waiting time against the various activities in the map. This helps to analyse whether an activity adds value to the business by seeing if that activity reduces cost, reduces duplication and improves customer service.
3. Show Process and Activity Owners
Process maps provide clarity for employees and managers regarding who is accountable and who is responsible for the process. With this information, process problems can be resolved quicker and employees and managers can have clarity regarding their responsibilities.
4. Support Induction and Training
Because process maps create a standard way of working, they are a great training tool for both old and new employees regarding best practice.
Take a look at a Triaster Process Library to see how employees can search for processes based on their job role.
5. Process Mapping Tools Make Life Easy
Your process improvement plan will only be as good as the Process mapping tools that you use. Paper-based process mapping may help you to see the current state of your processes, but without the data capturing capabilities of a process mapping and management tool, it will be extremely difficult to capture and analyse process data for the purpose of improvement.
A second important thing to note; process mapping tools need to be useful to your staff (accurate), usable by staff (easily accessible) and get used by staff (easy to use and understand).
However, if you get a process mapping and management tool that's right for your business, you will find that improving business operations becomes a whole lot easier.
6. Show Compliance and Continual Improvement
Process maps can be used to show compliance to regulatory standards such as ISO, FCA and SOX to name a few and will also serve as a valuable resource for internal/external audits.
If this is what you are looking for, make sure you have a process mapping tool that can demonstrate compliance with regulatory standards with a simple drag and drop search functionality.
7. Business Process Analysis: Identify and Mitigate Risk
Process maps can be used to identify levels of risk within the business and what controls are in place or need to be in place to mitigate the risk.
Visibility is priceless for understanding the most precarious steps in the process chain. This type of understanding allows an organisation to put safeguards around the process steps (such as requiring sign-off from management, following a checklist, leaving a note etc....) making it easier for the accountable employee to mitigate the risk.
8. Support Operational Excellence
Employees are able to find the answers themselves rather than asking for an explanation. Process maps can be simple in nature but can also contain:
- procedures
- guidance note/work instructions
- forms
- videos
- or anything that will help the employee to do their job
This means that an employee can look up the appropriate information, for the appropriate process at the appropriate time – making any working environment far more efficient.
6 Methods of Mapping
There are several ways of accurately capturing the process data that feeds the creation of a process map.
There is no 'one-size fits all' when it comes to process capture and one of these methods may be more in line with your culture or the structure of your organisation. I would also point out that it is often a combination of the following 6 methods that will prove the most valuable when trying to capture accurate process data.
1. Individual Staff or Small Group Interviews
This process mapping technique is used when the content of the process map is likely to be relatively straightforward, so only a small sample of those that perform the process are required (usually 1-3 people) to be involved in its definition.
Before the interview you will need to:
- Have a prepared set of topics you will be covering and questions you will be asking
- Make sure each session goes no longer than 1 hour
- Come back to a problem later if it is proving particularly difficult
- Never go over the session time – respect employee time and they will respect yours
During the meeting you will need to:
- Define the scope of the process to be captured (identify the start and end points).
- Capture the major steps involved (the Activities)
- Capture what is produced by each Activity (these are the Deliverables)
2. Facilitated Discovery Workshops
Use this technique when it is important to gain an accurate understanding of a process from a larger number of people (a maximum of 10 at the most). This is more suited to a less detailed process understanding but is necessary in cases where there are multiple process owners.
The same steps are necessary for small groups as they are for larger workshops but you will also need to:
- Work harder to involve people
- Keep as much energy, variation and interest in the workshop as possible
- Stick to the facilitation process and not engage in subject matter debate – leave that to the participants
- Lead the discussion by asking questions but let the room debate and agree on solutions.
3. Analysis of Existing Documentation
It is a huge time saver if a process can be
developed from your existing documentation alone – be careful though as they may not be accurate.This method is useful in established process environments where the aim of the mapping exercise is to modernise, reduce the documentation burden or review the existing management system rather than to create content from scratch.
4. Direct Work Observation
This method is usually more efficient in a highly manual business environment where the process steps can be overseen and tasks can be observed in real time (think of a packaging warehouse where an order comes through, a product is sourced, packaged and shipped to the customer).
5. Business Analysis Design
This is particularly useful in project start-ups where the process doesn't yet exist. It is also useful in environments where access to the process experts is not an option.
It is hard to get an accurate process without a process expert so if you are going to go ahead with this method then make sure you:
Don’t guess! If you cannot be sure, don’t make assumptions.
Get sign off from a process expert
6. Import of Existing Processes
Some Business Process Management systems can import existing process documentation into structured maps, but this is most difficult with unstructured sources such as documents, slides, video and spreadsheets.
Existing process maps can be imported from applications such as Microsoft Visio into more complex process management and improvement tools without making any changes.

Chapter 3 - The Key Components of Process Mapping Projects
The 'As Is' Process
The As Is represents the current state of your process and is the starting point for any improvement project.
Capturing your As Is will not tell you how to improve your process, but it will show you exactly what is going on in your business so that you can identify improvement opportunities moving forward.
The 'To Be' Process
The To Be process is the future (or improved) state of your process.
Once you have your As Is process mapped out, you can then start analysing it for potential improvement opportunities.
From these opportunities, you can model changes and create a To Be map that will eventually become the improved process.
End-to-End Process Mapping
End-to-end process mapping contains all the work that needs to be done to meet the process goal. This encompasses the very start of the process to the very end.
For instance, 'a customer places an order' might be the start of a process and 'a customer receiving an order' might be the end. An end-to-end process map would capture all the inputs and outputs from the start of that process, to the end.
The Levels of Detail
Process mapping tends to be captured in 3 or 4 levels of detail:
- Level 1 – Top level end-to-end maps: tend to be fairly simple with few branches
- Level 2 – Provides more detail than the end-to-end maps and covers a horizontal flow through an organisation. The complexity level can be high as they will involve multiple departments and handovers, possibly with iterations, branches and multiple outputs
- Level 3 – These tend to be aimed at individual users and have a lower degree of complexity than the level above.
- Level 4 – Bottom level maps: tend to be used for those processes that get re-used in multiple process flows and as such can be quite simple.
When deciding the level your organisation should map to, ask yourself a very simple question:
'Who is your audience and what do they need to see?'
Inputs and Outputs
When you break down a process to its core, it is a series of steps that is made up of:
- Inputs - Inputs are usually defined as the process activities. Activities have zero value because they encompass a cost (time, effort, money) that goes in to creating the output.
- Outputs -The output is what is produced. It is the result of time and effort and is the most important/valuable part of the process.
When process improvement is broken down to its simplest level, it is merely a series of inputs and outputs.
One method of Identifying improvement opportunities comes from evaluating the inputs and seeing whether they fall into the category of non-value adding (a step that has no value and can be removed) and necessary non-value adding (a step that adds no value but is crucial for producing the output).
The Symbols/Shapes Involved With Process Mapping
Values are assigned in process mapping through symbols/shapes.
Again, when looking at the most basic level of process mapping, inputs, outputs and decisions (a step in the process that can have multiple outcomes) are represented as different shapes in order to assign a visual value to the process. A square can be an input, a circle could be an output and a triangle could be a decision leading to multiple outcomes.
If you are capturing a process on a wall, in a meeting, surrounded by a team of people, you can use a large roll of paper as the canvas and different coloured post-it notes to represent the different symbols.
For instance, you could have green post-it notes for inputs, blue post-it notes for outputs and orange for decisions.
Below, I have laid out a simple process map created using the Triaster process mapping tool. As you can see, inputs are a different shape and colour to the outputs and you will also see that underneath each output is the job role responsible for that activity.
The Noun-Verb Method
Triaster has its own simple and unique process mapping methodology. For a full description of how you can use this in your process mapping, please look at our article explaining the Noun-Verb method.

Chapter 4 - Process Mapping Tips and Tools
Tips for Creating Useful Process Maps
There is a lot of information out there on process mapping and a lot of that information is not very helpful. The purpose of this guide, is to give you actionable insights into creating an effective process map and I have laid this information out as clearly as possible.
Over the years, Triaster has learned some best practices for capturing and visualising processes; here is a list of 4 tips for creating greater clarity:
- Optimising Clear and Useful Outcomes– the best improvement outcomes usually spring from constantly asking this question: "what does this activity produce?" - where is the value that necessitates performing the activity?
- Be Careful of the Language Used– An example of this is the input (Open box) and the output (box open). It is true, one is the task being performed and one is the result of the task, but process maps sometimes need more detail and you need to make sure that the phrasing works best for the employees who are accountable for perfoming the task.
'How to/Show me the' - this technique will help you describe the process step and make it obvious that it is an input or an output. Putting 'how to' in front of the input can clarify the appropriate way to formulate the language of the step. For instance, 'how to sales system updated with reference number' does not make sense but 'how to update sales system with reference number' does. Similarly, for the output, 'show me the sales system updated' doesn't make sense but 'show me the updated sales system' does.
- How Obvious is the Language Used? - You'll start to see by now that the language you use to create a process step is extremely important. You should avoid acronyms, ampersands, hyphens and full stops because they are confusing and complicate the simplicity with which the process mapping is trying to represent.
Following on from the language used in the maps, here are 5 simple tips for getting your employees on board the process improvement train:
- Make the Maps Easy to Access – Ensure that your process management system is accessible to all staff so that you can create a standard way of working for the business.
- Make the Maps Easy to Use – You're going to have a hard time implementing a new culture if your management system is difficult for your staff to use. Make sure the information is easily searchable and accessible by staff within three clicks.
- Make the Maps attractive to Use – Design is important; a well-designed management system, with a theme that is unique to the company, can do wonders for morale around a culture shift.
- Make the Maps Useful – I've said this a lot by now but process maps need to be all about ACCURACY! It also needs to be up-to-date and deliver the type of information that everyone needs.
- Tell Your Employees About it – and don't just send out a work email either. Break out the marching band and create a cultural event around your process improvement initiative. Communicate using:
- Leaflets and posters in communal areas
- Banners
- Company-wide email campaigns
- Giveaways and competitions
- Presentations
- Workshops and events
- Drop-in sessions
Different Tools to Map a Process
There are 4 common tools associated with process capture and mapping. These are:
Paper, Sharpie Pens and Post-it Notes – This is a particularly effective tool for capturing the process while running a process mapping workshop. This allows multiple subject matter experts to get into a room and discuss the right data to capture – and if you get a process step wrong, you can discard a post-it note and start again.
Microsoft Word and Power Point – both of these tools can be used to build flowcharts and allow you to build a basic process map using simple, pre-set shapes. This is a great tool for beginners but you will need something more expansive if you hope to process map an entire department or organisation.
Microsoft Visio – this is Microsoft's flowchart and diagramming tool, which will allow you to create simple process maps with a variety of shape templates. You can drag and drop these templates to create your process maps and create some limited data properties in conjunction with Microsoft Excel. Visio will take you a step further than the first two tools and although it is an extremely popular option for business process mapping, it is limited in its ability to interpret data and also lacks uniformity across the business.
Visio maps can and have been easily integrated into Triaster's management and improvement system when our existing customers identified a need for more accurate improvement capabilities.
Business Process Mapping, Management and Improvement – These are tools that are commonly used by larger businesses that wish to integrate their process mapping, management and improvement solutions into one product. For instance, at Triaster our process management and improvement system can import existing Visio process maps seamlessly and this creates a pathway for business improvement through:
- Modelling cost, effort and time data
- Displaying a full RACI (displaying which roles are responsible and accountable for the process)
- Modelling risk
- Creating a bespoke management system that can be designed to suit an organisation's unique way of working
- Making process maps easily searchable and accessible to all staff
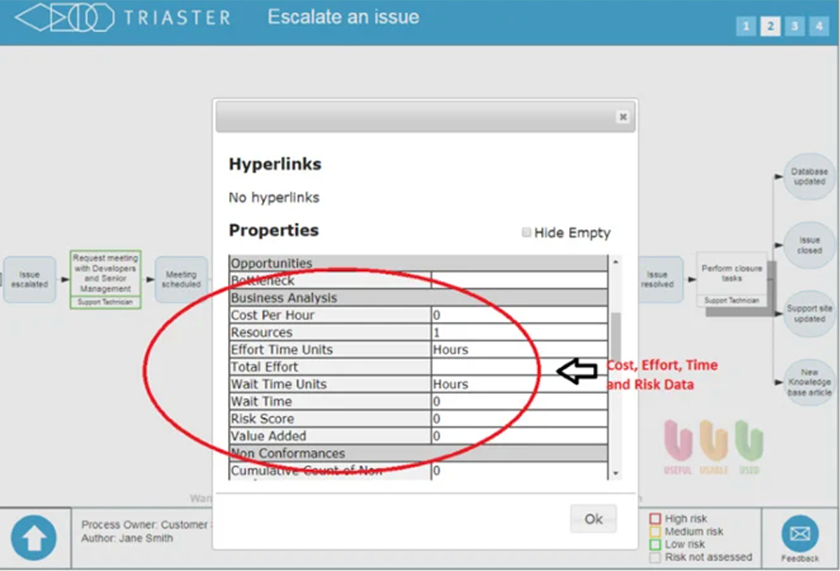

Chapter-5 - How to Process Map – a Step-by-step Guide
Organise a Process Mapping Workshop
Successfully capturing the correct process data starts with the organisation of a process mapping workshop.
For the workshop to be successful, you must already have:
- Agreed the scope of the information/processes to be captured (agree on a start and an end point)
- Decided the timeframe for the meeting and stick to it (this should be in line with the start and end point)
- Found out who are the Subject Matter Experts (SMEs) for the process (those who are Responsible, Accountable and need to be Consulted)
- Set up a meeting with those same Subject Matter Experts from the business area that you will be process mapping
- Someone present who has knowledge of how the process links to other business areas.
- Given information to all attending as to the background of the process mapping initiative and why it's key for the business (getting stakeholders on board is crucial)
- Provided clear and simple information
- Sent every participant an agenda for the meeting including how long the project will run, what you will need from them and the process you will be mapping (so they can prepare).
- Invited no more than ten people to a workshop.
- No more than 4 virtual attendees.
- Given everyone invited to the workshop an opportunity to ask you questions before the workshop starts
- Given the same opportunity to their departmental heads – if you don’t have the support of all of the relevant parties you'll want to uncover this as early as possible.
Run a Process Mapping Workshop
Once you've done all the pre-planning for your process mapping workshop, then it's time to capture the accurate information from process mapping experts.
Pre-planning is crucial to make sure that your workshop doesn't go off topic, become boring or lose focus.
The important steps to running a successful workshop are to:
- Get a large roll of Brown or white paper for the base of the process map
- Use three different types of post-it notes to represent the Activity (input), the Deliverable (output) and the Decision
- Use sharpie pens to write down the process steps as they are revealed in the workshop
- Make sure everyone can see how the process is being captured
- Lead the group to contribute to each process step (You will need to ask questions)
- Name the process (Example: Customer Sales Cycle)
- Define the individual steps involved in the process – this means understanding your Inputs (the Activity Performed) and Outputs (the deliverable result of the activity).
- Begin mapping by using post-it notes to mark the start point and end point of the process (both will be Deliverables, so both will be the same color post-it notes (Customer Sales Cycle Example: Start Point - Sales Enquiry; End Point - Quote)
- Get the output from every input by asking the question: "what does this input produce?"
- There must be an output after an input
Finalising and Creating Your Business Process Map
Once you have captured the information accurately from subject matter experts in the workshop, you'll need to create your process map.
For the final capture of information and creation of your accurate process map; make sure to:
- Import the data captured at the process mapping workshop into your process mapping software.
- Check that the process steps are labelled correctly
- Check that the process steps are complete - have you left anything out of the process?
- Check that the responsibilities of staff are clearly laid out in the process map
- Oversee the real process and check that it matches the one captured by the group.
- Identify any bottlenecks or process inefficiencies that can be fixed.
- Download the Process Mapping Checklist
To help you structure your process mapping as you go, I have included a link to this same checklist (in a downloadable format), which you can print and tick off as you complete each step.

Chapter 6 - Using Triaster for Continuous Business Improvement
Process Mapping and Improvement in Action: A Case Study
Before they turned to process mapping, New Charter Homes had 3 problems they were trying to address:
- The organisation faced a 15% reduction in revenue by 2019/2020
- A restructure was necessary, resulting in a lack of resources and being unable to deliver on paper-based processes
- The Service Improvement team wanted to improve tenant/customer satisfaction
The Service Improvement team eventually turned to process mapping for the answer and, after trialing and then purchasing Triaster software, New Charter mapped out the end-to-end processes of the entire tenancy lifecycle.
From here, they took 6 steps to capture accurate processes within their organisation:
- The Service Improvement team started with a process capture workshop, inviting all the key stakeholders for the Keys-to-Key process
- The team went on job-shadowing excursions to ensure that the processes as mapped were what actually happened in reality.
- As well as capturing the processes, the data was captured too. Using a bespoke properties file developed by Triaster, the team was able to automatically calculate the cost of every activity.
- The team then mapped the As-Is of the entire keys-to-keys process (about 280 process maps), which exhibited great potential for process improvement.
- Finally, New Charter's Service Improvement team completed the modelling of the TO-BE processes and investigated ways of replacing paper-based processes with mobile applications
- These mobile solutions were then specifically designed to address the New Charter Group's key challenges
From applying these 6 steps, New Charter has already saved £350k per annum – just through process mapping.
If you would like to take a more in-depth look at how process mapping and improvement can change your organisation for the better, take a look at how these 8 organisations (including New Charter) used Triaster software to improve their business efficiency and reach sustained, measurable improvement.
Triaster's Process Mapping System
Triaster has been invested in Business Process Management and improvement for over 20 years. In that time, we have refined our process mapping and improvement software to a point where it can capture, analyse and report on data to demonstrate wasteful processes and inefficient activities.
Process mapping in itself is a useful tool that will capture the process you currently perform so that you can look for improvement opportunities. But if you want to experience the type of efficiency gains and financial returns that an organisation like New Charter has experienced, then you are going to need a software system that can accurately capture your process information, store it in one place (where it is easily accessible and searchable for all staff), and model improvement scenarios to mitigate risk and continually improve an organisation.
Process mapping can be as simple as using a flow diagram on Microsoft Word or as complex as multiple levels of process data that visualises time, effort and cost for every single process step – it all depends on what you are looking for.
Simple process mapping with tools like Visio can be great for those that want to start slowly and dip a toe in the process improvement pool, but it will not give you the type of control, scope and efficiency gains that a dedicated business management system can.
It can be difficult to find the approach that is right for you and your organisation, but if you would like to discuss it further, we can advise you on an approach for your business, whether it be creating isolated process maps, or a management system which is purpose built to create a culture of business improvement.
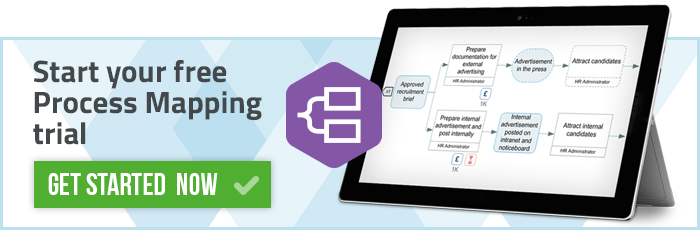
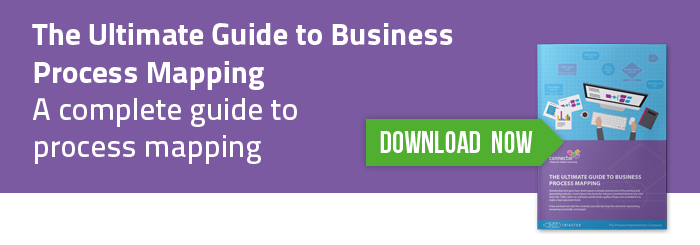